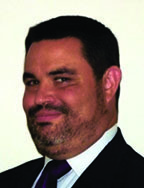
This series of articles was published in the May/June 2019 Grain Journal.
Like almost anything in the workplace, the establishment of a safety culture requires the combination of management commitment and employee engagement.
Role of Management
Managers establish a safety culture by setting safety as an organizational priority. They are responsible for creating a workplace environment where safety, production, and quality intersect. Needless to say, they must lead by example.
Specific to safety, management’s role includes:
• Support. Managers must allow time to execute a safety program and allow time for it to succeed.
• Direction. Managers evaluate and manage data related to safety and use that information to create an environment where employees can succeed at safety.
• Ownership. Managers make sure that all the elements of the safety process occur, remove obstacles to practicing safety, and ask employees for feedback regularly.
Role of Employees
• Employees must be involved in the creation of the safety process.
• Employees must have the sense that safety is being done with them, not to them.
• Employees must have a formal means of being involved in safety. This could include being part of a safety committee or taking part in near-miss reporting, among other things.
• Employees must see the results of their actions.
Employee Engagement
The above are good goals for employees, but for them to work, employees must be engaged in safety. Here are some reasons why employee engagement is important:
• Engaged employees care more about the company, their jobs, and their performance.
• Engaged employees use more discretionary effort.
• A study at one company that has a grain (barley) handling division, Molson-Coors, showed that engaged employees were seven times less likely to be injured than non-engaged employees.
• Engaged employees are much more likely to be ethical and driven.
• Engaged employees are the source of innovative solutions.
A number of factors drive employee engagement:
• Employees perceive the importance of their jobs.
• They understand the vision of the company.
• They clearly understand what is expected of them.
• They are allowed a degree of self-determination and empowerment in the workplace.
• Behavior results in consequences designed to focus employees on the workplace.
• Employees have a sense that the workplace has integrity.
• There are opportunities for advancement.
• Employees engage in high-quality relationships.
• Management promotes excellent feedback, dialogue, and communication.
• The organization is focused on safety process rather than safety outcomes.
Practices to Promote Engagement
These are must-dos for managers to promote employee engagement in safety:
• Help employees understand that their input is critical.
• Look for reasons to act on employee suggestions and not avoid them.
• Make the employee part of the solution, not the problem.
• Pass on all credit to the employees for their actions.
• Avoid a “rule-based” approach to safety.
THE ROLE OF A SAFETY CULTURE
One witty description of what safety culture is could be “what employees do when no one is watching.”
A more conventional version of that is “the beliefs, actions, behaviors, values, and traditions of safety activities for a company tied together with a historical context.”
A company’s safety culture comes from a number of sources:
• The company’s larger organizational culture.
• The founder effect – what were the founder’s beliefs and actions with regard to workplace safety?
• Regional and societal norms.
• Grain and/or feed industry specific values and traditions.
• If already in place, an environmental- or objective-driven culture.
• The preferences of management.
Experts in the field generally agree that a safety culture has the following characteristics:
• It is observable.
• It is quantifiable.
• It is very self-sustaining.
• It is an antecedent to behavior – safe behavior can be attributable to the existence of a safety culture.
• It is a different concept from a safety climate.
Strong Safety Culture
Here are ways to tell if a workplace has a strong safety culture:
• Management consistently sets an example.
• There is a lack of organizational arrogance (“We’ve always done it that way”). This is different from pride.
• The workforce is empowered to make meaningful contributions to safety.
• Employees are highly engaged.
• There is a clearly defined balance between production and safety.
• The workplace has high-functioning safety committees.
• The company has a well-written safety mission statement.
• An effective professional is in charge of safety.
Weak Safety Culture
A workplace with a weak safety culture is characterized by using only lagging indicators to measure performance. Here are problems associated with lagging indicators:
• They measure only failure rates.
• They manage safety by looking at what has happened, not what will or might happen.
• They may encourage employees to hide injuries.
• The recordability or severity of a safety incident is influenced by many factors after the event.
If you want positive change on workplace safety, it’s important to be like a coach. Don’t watch the scoreboard. Watch the action on the field.
Workplaces with a weak safety culture use punishment in accountability standards. Punishment does not reinforce anything. Instead, it becomes part of a repeating cycle. Ask yourself, has the use of punishment ever inspired anyone?
Focus on Processes and People
Improving safety culture is done by creating specific initiatives to enhance the weaker elements of safety systems in the workplace. Then, establish metrics that measure the progress achieved on those issues rather than looking at the outcomes obtained. Finally, celebrate the successes.
Always look for opportunities to include employee suggestions and ideas.
Punishment cannot be removed completely from the system. Some employees will push the envelope or out-and-out violate safety rules. However, the role of punishment in the workplace can be minimized. Blame is never beneficial.
Changing a culture of accountability to a system of acceptance, support, empowerment, and reinforcement is difficult. But providing critical feedback and coaching is much more beneficial and should be used as the standard response first and foremost.
PRINCIPLES OF ENGAGEMENT
Achieving employee engagement in a strong safety culture is a long-term and often difficult process, but certain practices can help.
• Always do safety the right way.
• Ensure the company adopts a relentless desire to incorporate safety into every aspect of the business.
• Make sure work is done safely at all times, not just when someone is looking.
• Move beyond compliance and blame.
• Optimize behavior, culture, and safety measuring systems.
• Ensure that all elements of safety are integrated and practiced with integrity.
Traditions
Traditions may represent the ultimate manifestation of the workplace culture. But that is not always a good thing.
Are those traditions productive toward creating a strong safety culture, or are they harmful or limiting? Are employees resistant to change when needed?
As a program to improve employee engagement proceeds, it will need to be re-evaluated from time to time.
Questions to ask: Have the initiatives improved the culture? Are employees actively engaged in the safety process? Do they want to be? Are viewpoints more closely aligned?
The Value of Engagement
Benefits from engaged employees are that they:
• Are more successful.
• Are safer.
• Look out for the safety of others.
• Are the best sources of information.
• Will do what it takes to make your company successful.
Conclusion
Understanding what safety culture is, how it drives behavior within your company, and how to continually strengthen your safety culture is critical. Having engaged employees who actively participate in safety and work in a communication-rich environment is the formula for achieving world-class safety performance.
This series of articles is based on information from a Dec. 4, 2018, webinar hosted by the Grain Elevator and Processing Society (GEAPS) and presented by Chris Goulart, senior loss consultant with Aon, an insurance broker and professional services company based in Lincolnshire, IL (847-295-5000). The webinar can be viewed free at grainnet.com/safetyengagement.