Protect Against Exposed Inward-Running Pinch Points
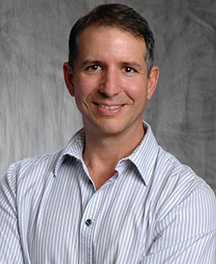
Open belt conveyors are still used in many operations throughout the grain handling industry. An open belt conveyor consists of a rubber belt set on rolling idlers, wrapped around a steel drum at each end, and driven by a large motor.
They contain a multitude of rotating parts including idlers, drive shafts, and pulleys. Rotating parts operating at high speeds pose entanglement hazards and inward-running pinch points.
Pinch points are present where the belt touches equipment such as drive pulleys, snub pulleys, and idlers.
Should a worker’s limb be pulled into the equipment during maintenance or cleaning activities, the worker can become trapped between the belt and the equipment.
Loose clothing or tools also can be pulled into the equipment before a person can react and let go.
A worker’s exposure to severe injury increases when cleaning material around or from the components of the conveyor system. Cleaning activities place the worker in close proximity, often an arm’s length or closer, to the conveyor.
Tools such as shovels or brooms function as extensions of the arm and can easily become caught and pull the worker into a conveyor. Maintenance activities also require workers to position themselves in close proximity to the conveyor’s hazard zone.
No Time to React
A conveyor belt moves at a constant speed between 100 to 1,968 feet per minute (0.5 to 10 meters per second). Consider the following example: An Olympic sprinter has an estimated reaction time of 0.18 seconds when at the starting line and totally focused on the race. If the sprinter becomes entangled in a conveyor belt traveling 300 feet per minute (1.5 meters per second), the athlete will be carried approximately 10.6 inches before they even realize what has happened.
Research indicates that reaction times can increase by a factor of two or three when distracted. When a tool – such as a shovel – gets pulled into a conveyor, the natural reaction is to tighten the grip to retrieve the tool, resetting the reaction time. Based on these factors, it is easy to see how a worker, who is not an Olympic sprinter, could be caught inadvertently in a nip point between the belt and a carrying idler, or the belt and a head or tail pulley. It is impossible for a worker to react quickly enough to avoid being drawn into the equipment.
Avoiding Pinch Points
The good news is that there are best practices employers can implement to prevent these incidents. These include:
• Develop a plan to replace open belt conveyors over time with enclosed units. This eliminates exposure to the moving belt and associated parts as well as reducing fugitive dust.
• Ensure that inward-running points at tail pulleys, idlers, and V-belts are guarded properly.
• Install removable or adjustable barrier guards along the open sides of the conveyor.
• Install crossover platforms to eliminate the temptation to step on belts to cross to the other side. If workers walk under conveyors to access working areas, make sure the bottom side of the conveyor including the belt and idlers are guarded.
• Equip open belt conveyors with audible alarms that warn employees at startup.
• Equip open belt conveyors with safety equipment, such as emergency stop cords or e-stop devices, that are labeled and visible along the conveyor.
• Ensure that open belt conveyors are locked and tagged out when employees are exposed to moving belts, pinch points, and entrapment hazards during routine cleaning and maintenance. Lockout/tagout procedures also should address belt tension.
• Operate conveyors within their design capacity. Exceeding these limits can lead to equipment failure and spillage. The resulting cleanup activities can expose workers to equipment hazards.
• Ensure that areas adjacent to open belt conveyors are free of debris, tools, and material that can cause workers to slip or fall into the conveyor’s hazard zones.
• Ensure that employees avoid wearing loose clothing, such as hooded sweatshirts with draw strings, or other wearable equipment, such as fall protection lanyards, which can be pulled into rotating equipment.
• Routinely train employees on conveyor hazards and safe work practices when working on, under, or adjacent to open belt conveyors.
• Perform a hazard analysis prior to working on or near open belt conveyors.
There may come a day when open belt conveyors are a distant memory, but that day is still far off. In the meantime, please share the information in this article with your employees. We must all do our part to send them home safely.
References
Martin Engineering Company. (2016). Foundations for Conveyor Safety. Worzilla Publishing Company. https://foundations.martin-eng.com/book-form-download-page?hsLang=en.
Joe Mlynek is president and safety and loss control consultant for Progressive Safety Services LLC, Gates Mills, OH; 216-403-9669; and content creation expert for Safety Made Simple, Olathe, KS.